Flying robot cart introduced for better human-controlled cargo handling
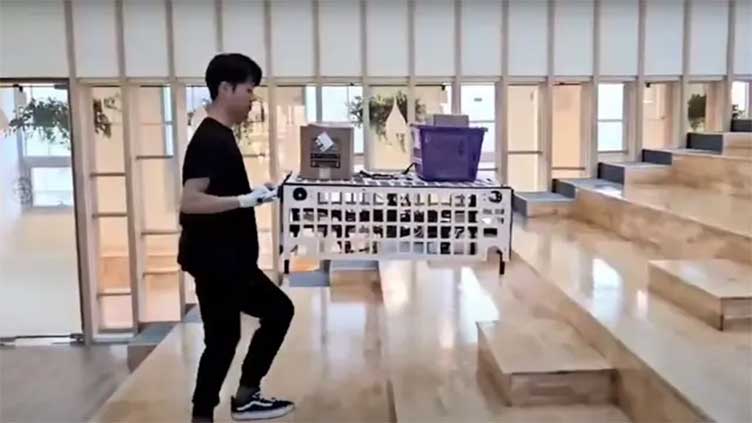
Technology
It can fly over obstructions like staircases
(Web Desk) - Researchers have introduced a flying cart, which they deem a new cargo transport system that works based on physical human-robot interaction.
The system, developed by a team at Seoul National University of Science and Technology (SeoulTech) in Korea, is powered by a novel, fully actuated multirotor platform called Palletrone.
The platform features a handle at the back that resembles a shopping cart, and a huge flat area on top for simple freight loading.
Palletrone’s flight is operated by a person grasping the handle and exerting force in various directions to keep the cargo steady and not tilt while in flight.
The team uses an admittance control technique with a disturbance observer algorithm for simpler force estimation.
Researchers analyzed flight stability and performance under varying cargo loads, showing that individuals can effectively control the system through applied forces in tests.
Due to their capacity to move in all directions, multirotor unmanned aerial vehicles, or mUAVs, are developing from basic aerial photography instruments into adaptable robots for moving freight and equipment.
According to the team, “Aerial Physical Interaction” (APhI) missions, in which people can physically direct the mUAV’s flight, are gaining more attention. Because of this, the mUAV can be maneuvered like a shopping cart, which makes it perfect for moving cargo across locations like factories or malls.
Unlike wheeled carts, mUAVs can fly over obstructions like staircases. The current approaches involve direct contact or the use of tethers, each with benefits and drawbacks, including safety issues.
Researchers suggest a novel human-robot interaction-based aerial cargo transport system as a solution to this issue. The study introduces advanced flight hardware for stable cargo movement and a new controller design that allows easy human control of the flight.
Palletrone’s design includes a cubic, protective enclosure for safe airflow and cargo loading. It has eight actuators (four propellers and four servo motors) for precise control in all directions.
The new design developed by the team also includes a handrail for human interaction and a larger platform for better cargo capacity.
The Palletrone drone ensures a flat and stable platform by maintaining zero roll and pitch, even with unevenly loaded cargo. It responds to user input through its IMU, translating small touches into control over its movement in horizontal, vertical, and yaw directions, according to IEEE Spectrum.
A key challenge is distinguishing between forces from cargo and the human operator, as both can affect the drone’s movements. However, the team claims that they’ve developed a simple method to differentiate between them.
To avoid cargo spilling, the drone uses internal propeller arms that vector thrust in any direction. Despite concerns about airflow, its porous side structures ensure sufficient thrust, with only a 5 percent decrease when the top is fully covered.
The current version of the Palletrone requires user control, though it can maintain its position if released. Researchers compare its operation to steering a shopping cart. While it can carry about 6.6 pounds (3 kilograms), it’s not yet suitable for heavy loads like grocery bags.
The team envisions the Palletrone being used not just for logistics but also as a flying tripod by attaching a camera. “This would be particularly useful in environments where specialized filming equipment is difficult to procure,” said Seung Jae Lee, assistant professor of mechanical system design engineering at SeoulTech, told IEEE Spectrum.
The present study makes the assumption that human operators are the only source of disruptions, which may not be true in real-world settings where the system may also be impacted by wind and gusts. Future research must determine human goals in the midst of these diverse disruptions.
Furthermore, pHRI flight performance has primarily been assessed qualitatively through the use of Bode plots and frequency response analysis. To satisfy these standards, motion control should be optimized, and quantitative evaluation criteria should be established in future studies.