Giga-casting and robots: How Volkswagen's Trinity aims to catch up with Tesla
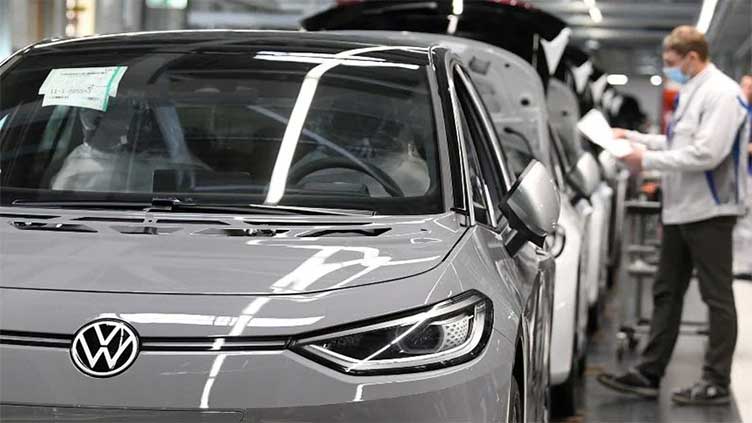
Technology
Giga-casting and robots: How Volkswagen's Trinity aims to catch up with Tesla
BERLIN (Reuters) As Tesla Inc. begins production at its German plant this month, rival Volkswagen Group is weeks away from finalizing plans for a 2-billion-euro ($2.2 billion) electric-vehicle factory that it hopes will bring it up to speed with its U.S. rival.
Tesla says it can already produce a Model Y crossover in 10 hours at its new factory in Gruenheide near Berlin, whereas it can take VW three times as long to make its ID3 full-electric hatchback.
VW now aims to slash production times at its new Trinity plant by using techniques such as large die casting and cutting the number of components in its cars by several hundred.
The factory should be up and running in VW’s home city of Wolfsburg in 2026. It will build a full-electric sedan for the VW brand with advanced self-driving capabilties.
"Our goal is clear: we want to set the standard with our production," VW brand production chief Christian Vollmer told Reuters in an interview. "If we can get to 10 hours, we have achieved something big."
The automaker has been improving productivity at a rate of about 5 percent a year but must take bigger leaps to keep its upper hand in the European market, Vollmer said, without providing a new percentage target.
VW -- with its stable of brands from Skoda, Seat and VW to Audi, Porsche and Bentley -- has a 25 percent share of the European EV market, ahead of Tesla on 13 percent.
But the pressure on German automakers to both master and ramp up EV production has been intensified by Tesla’s presence in the country and VW Group CEO Herbert Diess has warned Germans must speed up to avoid getting beaten on their own turf.
Giga presses
VW’s goals align with a wider trend in the industry of simplifying product ranges and streamlining production as automakers scramble to find the cash to fund the electric transition - and keep up with rivals like Tesla that do not have to juggle making EVs as well as cars with combustion engines.
"Tesla really ignited the drive for reducing part counts and making simpler products," Evan Horetsky, a partner at McKinsey who was formerly in charge of engineering at Tesla’s new Brandenburg plant, said. "Legacy manufacturers have a more difficult time because they have to maintain current orders."
A Tesla spokesperson said one of the reasons it can produce its Model Y vehicles in Germany within a 10-hour time frame is because it is uses two giant casting presses, or giga presses, applying 6,000 tons of pressure to make the rear of the car.
Tesla s Gruenheide press shop can produce 17 components in under six minutes. With six more giga presses on the way, Tesla will soon be making the front of the car with the giga press too.
"That is why we are so fast," the spokesperson said.
The giga casting technique that VW plans to adopt was popularized by Tesla as an alternative to the more labor-intensive method of assembling multiple stamped metal panels with crumple zones to absorb energy during a crash.
BMW has rejected large castings in the past on the grounds that the higher costs of repair outweigh the lower manufacturing costs.
But advocates say automated driving technology will reduce the frequency of accidents: "Tesla is designing a vehicle that most likely will not be in a severe crash," Cory Steuben, president of manufacturing consulting firm Munro & Associates, said.
Idra, the Italian company that produces giga presses, has declined to say whether it is working with Tesla, despite industry insiders confirming that the automaker s German plant uses their products to create the front and rear underbody platform for the Model Y.
In a recent interview with Automotive News Europe, Idra CEO Riccardo Ferrario said that VW and Volvo were the automakers that are closest to deciding on whether to move to megacasting for their future vehicles.
While VW can produce certain models such as the Tiguan or Polo in 18 and 14 hours in Germany and Spain respectively, its ID3, made in Zwickau, a factory juggling six models from three VW brands, still takes 30 hours to put together.
At the Trinity plant, multiple work steps will be condensed into one through automation, shrinking the size of the body shop and reducing the number of jobs requiring uncomfortable physical labor, Vollmer said, calling it an expansion of "human-robot cooperation."
VW does not plan to have giga presses at the new Trinity plant in Wolfsburg and will instead use the equipment at its factory in Kassel about 160 km (100 miles) away and transport the products by train.
U.S. investment bank JPMorgan predicts that Tesla s Gruenheide factory will produce about 54,000 cars in 2022, 280,000 in 2023 and then 500,000 by 2025.
VW, which delivered about 452,000 battery-electric vehicles globally last year, has not yet set an output target for Trinity, which will use its Scalable Systems Platform.
It aims to build 40 million vehicles worldwide on the new platform - which combines multiple internal combustion engine and electric platforms into one – with half of its global output all-electric by 2030.
Tesla, which produced 936,000 cars last year, has said it aims to put 20 million on the road a year by the end of the decade, or roughly double the current annual production of Toyota.
Still, Tesla can expect numerous challenges as it expands in Germany, from securing more water supplies to environmental groups angry about light pollution and congestion near the plant to unions worried about a management-heavy works council and wages being driven down by workers coming in from elsewhere.
"Starting production is nice, but volume production is the hard part," Musk told a cheering audience at a festival at the plant site in October 2021. "It will take longer to reach volume production than it took to build the factory."