Banana-based biomaterial to make parts for cars, bicycles
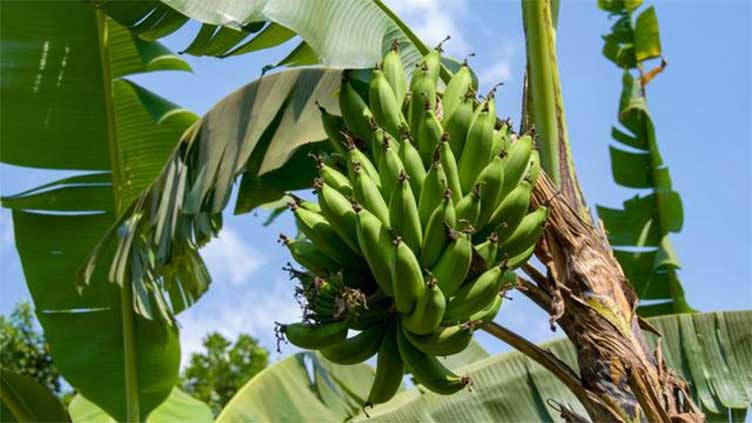
Technology
Fiber is extracted from the stem or trunks of banana trees
(Web Desk) - Akin to natural sources of fibers like coconut, flax, and hemp, bananas are another source that scientists have tapped to yield bio-based material for composite reinforcements.
The research was undertaken by the University of Maine System, Oak Ridge National Laboratory (ORNL), and the University of Tennessee, Knoxville, as part of an undergraduate research initiative.
Research students developed the banana material under the supervision of Cait Clarkson and Amber Hubbard, both ORNL R&D associate staff members in the Sustainable Manufacturing Technologies group.
The application of banana-based material was developed by Sustainable Manufacturing Technologies group.
The aim was to minimize the reliance on traditional materials such as glass fibers, carbon fibers, or metallic alloys which can be more resource-intensive and have a significant carbon footprint.
The new banana biomaterial is renewable, biodegradable, and possibly less energy-intensive to process.
“We went through the whole stages of a research project in one summer,” stated Emma Drake, a junior chemistry major at Auburn University who Hubbard mentored last year.
“I was able to get a bunch of really cool experiences both looking at analytical techniques and the extent of their chemical modification.”
The potential applications of sustainable material can be used as a composite reinforcement in automotive parts, bicycle parts, and other structural components.
The material offers lightweight yet strong components for vehicles even interior panels and other structural segments.
“You really wouldn’t expect it when you look at a banana tree,” says Brianna Greer, an undergraduate research intern at the Department of Energy’s Oak Ridge National Laboratory in the summer of 2023.
“You just wouldn’t think of it as a bicycle part,” she expressed.
The fiber is mainly derived from the stem, or trunk of the banana plant. They’re cleaned and dried then formed into fiber bundles.
Since bananas are squishy, especially in their ripe state, therefore, it’s harder to make fibers for composite reinforcements from that but banana trees are hard and comprise long, tough fibers that can boost strength in the material.
The material developed was under a Sustainable Materials and Manufacturing Alliance for Renewable Technologies, or SM2ART, program. This is part of a collaborative effort between ORNL’s Manufacturing Demonstration Facility and the University of Maine, funded by DOE’s Advanced Materials and Manufacturing Technologies Office.
Hubbard explained that the idea is to essentially develop their skills and their experience working with bio-based materials, additive manufacturing, and digitization for sustainable manufacturing overall.
“The goal is to bring students from all over the country and have them have experiences here at ORNL or the University of Maine,” she added.
Drake worked on the chemistry of the material and made surface modifications to cellulose.
“I’ve never really done a formal presentation in that kind of setting before, so getting that experience was really helpful,” she says.
As per the statement, the aim was to reduce the water uptake as water absorption impacts the fiber’s properties and performance.
The researchers successfully produced a “bicycle wheel well reinforced with banana fibre.”